Fuel Source and Burner Flexibility |
Standard or engineered burner configurations are available for use with both traditional and alternative fuel sources. Low emissions burners can be supplied to meet all emission requirements (e.g., Low NOx, Best Available Control Technology). |
Advanced Control Systems |
Complete control systems are engineered to optimize system safety and performance. Sigma thermal can supply simple and cost effective standard panels, as well as full process automation and PLC based combustion control / BMS. |
Coil Configuration Flexibility |
Coil flow path and metallurgy are engineered for each customer’s process requirements. Sigma Thermal has extensive experience in process coil design for multi-phase fluids, viscous hydrocarbons, suspended solids, and various gaseous mixtures. |
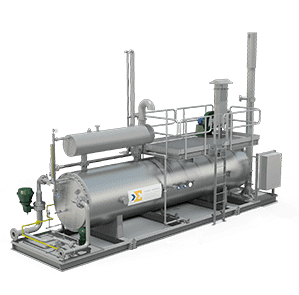
Water Bath Heaters
In the oil and gas industry, water bath heaters are commonly used for heating crude oil for refinement and natural gas conditioning. Water bath heaters are typically suited for applications where the outlet process temperature is no greater than 189 °F.
Two common subtypes of water bath heaters are salt bath heaters and direct-fired reboilers.
The principles of operation of a salt bath heater are similar to that of a water bath heater. A fire tube burner is submerged at the bottom of the heater vessel with a process coil submerged at the top. In lieu of water or water-glycol, a molten salt is used. Molten salts can be used at much higher operating temperatures, as high as 1,000 °F. The higher operating temperature capability does come with challenges. The freezing point of these salts can be close to 300 °F.
Direct Fired Reboiler
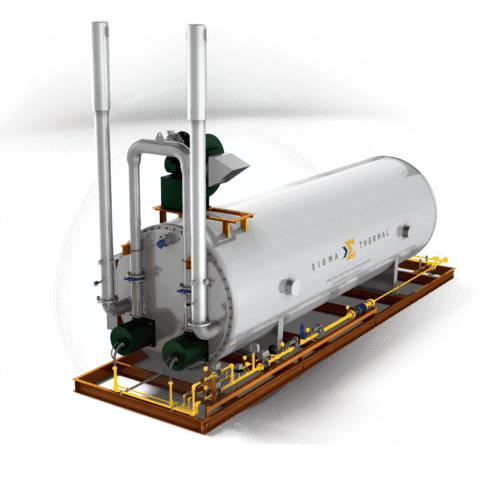
Sometimes referred to as a weir bath heater, this is a slight variation of a traditional water bath heater that does not utilize a process coil. This type of heater is most commonly used as a direct-fired reboiler for amine and glycol solutions. The bath vessel contains a fire tube and a weir at the end of the fire tube. The process fluid is circulated through the bath vessel in direct contact with the fire tube. After the process fluid is heated, it falls over the weir, where the return line sends it back to the process user.
Features & Benefits
- No potential for direct contact between the products of combustion and the user process: Safe operation for combustible or hazardous processes
- Flexible operating temperature and pressure range: Atmospheric operation for low-temperature applications
- No fluid or energy loss to make-up water, steam traps, or blow down: Savings in maintenance and energy costs relative to typical open loop steam systems
- Many burner and fuel source options: Force draft fire tube burners can be utilized for high efficiency and low NOx requirements
Design Features
- Fuel Source and Burner Flexibility: Standard or engineered burner configurations are available for use with both traditional and alternative fuel sources. Low-emission burners can be supplied to meet all emission requirements (e.g., Low NOx, Best Available Control Technology).
- Advanced Control Systems: Complete control systems are engineered to optimize system safety and performance. Sigma Thermal can supply simple and cost-effective standard panels, as well as full process automation and PLC-based combustion control/BMS.
- Coil Configuration Flexibility: Coil flow path and metallurgy are engineered for each customer’s process requirements. Sigma Thermal has extensive experience in process coil design for multi-phase fluids, viscous hydrocarbons, suspended solids, and various gaseous mixtures.
What Are the Components of Water Bath Heaters?
Our industrial water bath heaters are comprised of three main parts: the heater shell, fire tube, and process coil, each one designed according to your standard or custom package.
Heater Shell
We construct each bath heater shell out of carbon steel, a strong and durable material that can withstand high temperatures and prolonged processing cycles. Featuring two saddle-type supports, the shell holds the fire tube and the coil—installed in the shell from opposite ends—and the water bath itself.
Fire Tube
Water bath heaters have one or multiple U-shaped fire tubes that sit low in the shell. Because the fire tube assembly is low within the tub, it can more efficiently heat the fluid and bath system. We build our fire tube assemblies from heavy-walled pipe and attach them to the shell through a flanged end plate.
Process Coil
The process coil is a positive pressure unit that attaches to a flange end plate and sits above the fire tube in the hottest part of the bath. This provides the maximum possible energy efficiency while transferring heat. To guarantee product quality, each process coil assembly is 100% radiographed, made from seamless pipe materials, and compliant with ASME Section VIII, Div. 1 standards.
Our team can help you select the right standard or custom-size options to meet the needs of your operations.
How Do Water Bath Heaters Work?
All three major parts of the industrial water bath heater—the shell, the fire tube, and the process coil—play a vital role in the heating operations. Here’s how bath heaters work:
- The fire tube assembly, which is fixed in the lower portion of the bath’s shell, heats up by burning fuel oil or fuel gas.
- As the fuel burns, it releases heat that travels through the pipe walls of the fire tube, heating the bath to the right temperature level.
- Product fluids enter the bath through the process coil at the top of the shell. The fluid, which could be crude oil, natural gas, or other process fluid, absorbs heat from the hot water bath through the process coil’s walls.
- The fire tube assembly continues to heat the bath, and the heat temperature controller maintains the temperature over time based on the process requirements. The maximum advisable temperature in many baths is 189 °F. However, it’s generally best to operate below this temperature to both save on fuel consumption and allow for better liquid recovery during the subsequent processing stages.
What Are the Applications of Water Bath Heaters?
Sigma Thermal is a leading industrial water bath heater manufacturer that produces equipment for a wide range of heating applications, such as:
- Heating natural gas to prevent expansion valves from freezing
- Heating process fluids to make filtration and separation more efficient
- Keeping crude oil above the paraffin pour point
- Ensuring hydrate prevention
- Superheating or vaporizing LPG and LNG
- Heating crude oil or other sensitive fluids to reduce viscosity
- Regeneration gas heating
- Heating transfer fluids