Category Archive: Thermal Fluid Heating Systems
Click to Expand

As closed-loop systems, pre-engineered thermal fluid systems provide a source of heat for various industrial processes. They achieve effective and efficient heat transfer through continuous fluid circulation. These alternatives to steam boilers offer optimal temperature control, reliability, and versatility, reaching high temperatures but operating at low pressures. They’re compatible with a wide range of industrial applications in a variety of industries.
Thermal fluid systems are made up of multiple important components, all working together to heat and cool products and maintain appropriate process temperatures. Learn more about these various components, and the parts they play in thermal fluid system operations.
Heaters
One of the main components of a pre-engineered thermal fluid heating system is the heater, which raises the temperature of the thermal fluid per the needs of the application. System options include electric or gas-fired heaters. Electric heaters circulate process fluids around the system’s electric heating elements. They utilize electricity to raise the temperature of the thermal fluid rather than fuel oil, natural gas, or biomass fuel. Fired heaters are available in horizontal as well as vertical configurations, using flue gas to achieve the necessary temperature in the system’s coils and thus requiring minimal insulation. Both options come in an array of sizes and power capacities.
Burners
The heat load and size of the combustion chamber for your system will vary based on the thermal fluid system’s size and the type of process fluid it utilizes. Burners assist a system in handling the necessary power demands, heating thermal fluids prior to passing them throughout the system. When purchasing a pre-engineered thermal fluid system, your provider should be able to help you select the appropriate burner based on system size, the needs of your specific project, and other contributing factors.
Pumps
Another component to consider is the system’s pump, which circulates the thermal fluid at a constant flow rate though the system. While the flow rate of the fluid through the heater is always constant, the flow rate can be varied through the heat consumers using flow control valves. The return temperature to the heater will vary depending on how much energy the heat consumers are using, and the burner will modulate to provide a constant supply temperature regardless of how the return temperature varies.
When selecting pumps for a thermal fluid system, the following considerations should factor into your decision:
- Application: Pumps for thermal fluid systems are application-specific components. You can’t sub in standard hot water or boiler feed pumps for a thermal fluid system pump. Depending on your needs, you can choose from options like magnetically coupled pumps, water-cooled pumps, air-cooled pumps with mechanical seals, or API pumps, among others.
- Material: Pumps are available in various material constructions to ensure they’ll be compatible with the necessary thermal fluids and operating conditions. For example, alloy steel is an optimal choice for positive displacement pumps, but types like centrifugal pumps typically include cast iron or ductile iron wetted components.
- Pump Size: The size pump that you select must be compatible with the system. The right sizing will be dependent upon your system’s potential for pressure loss as well as the thermal fluid’s gravity when it’s at operational temperature.
Expansion and Drain Tanks
Valves
Thermal fluid systems must also use the right valves to operate. Valves must be resistant to leaking and wear at the high operating temperatures they will be exposed to Sigma Thermal recommends bellow-type seal for both manual and automated valves when operating at elevated temperatures. Bellows seal globe valves are more expensive that other types of high temperature valves, but they are also more effective and reliable for thermal oil, particularly at temperatures over 500F.
Control Panels
You also need the right control panel for your system to facilitate efficient operations. In conjunction with a system’s heater and all of it’s associated instrumentation, control panels enable you to continuously monitor all of the important system variables, safety functions, and control functions. This includes flow rate, thermal fluid temperatures, thermal fluid level, and exhaust gas temperatures for gas fired systems.
Simple and cost-effective control systems are available, as well as programmable logic controller (PLC) based systems that provide high-level functionality and communication with other plant systems.
Learn More About Thermal Fluid Systems
Specializing in industrial process heating solutions, Sigma Thermal handles thermal fluid system design, engineering, servicing, and training for customers worldwide. We offer electric and oil-fired systems in pre-engineered and custom-built options to best suit your needs. Our systems are simple yet robust, providing efficient, reliable temperature control. They’re easy to install and require minimal maintenance to deliver consistent and safe process heating with minimal downtime for your operation. Request a quote today to start your project.
Water bath heaters are a well-established method of heating gas and oil, however, in specific applications, a thermal fluid system can provide more significant benefits and improved performance.
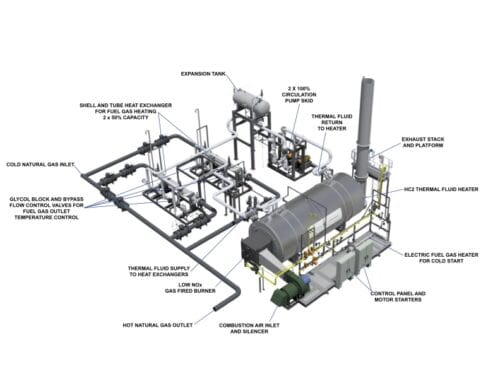
In this blog post, we will explore the unique advantages hot oil heating systems provide, including the following:
- Improved efficiency
- Reduced costs
- More responsive control
In the following sections, we’ll delve deeper into each of these benefits, uncovering how hot oil heating systems can streamline your industrial operations.
Click to Expand
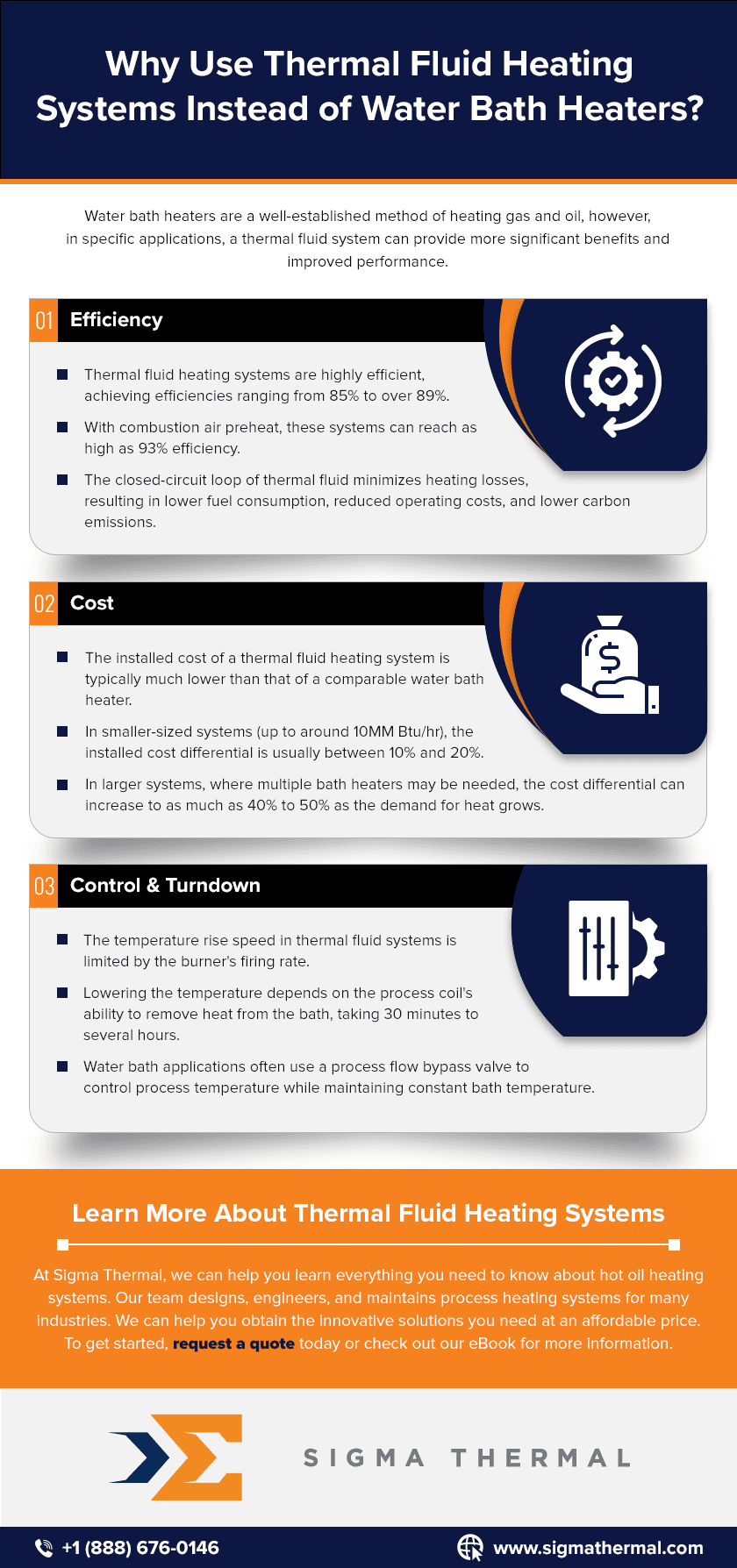
Efficiency
Thermal fluid heating systems are highly efficient. Today’s systems achieve efficiencies ranging from 85% to over 89%. When combustion air preheat is used, they can even reach as high as 93%. In addition, since thermal fluid systems feature a closed-circuit loop of thermal fluid, any unused heat flows back through the system, resulting in minimized heating losses. Higher thermal efficiencies like these result in lower fuel consumption, reduced operating costs, and lower carbon emissions.
Cost
The installed cost of a thermal fluid heating system is typically much lower than a comparable water bath heater. As the demand for heat grows, the cost differential grows also. In smaller-sized systems of up to around 10MM Btu/hr, the installed cost differential is usually between 10% and 20%. In larger systems, installing multiple bath heaters may be necessary to achieve the same performance as a single thermal fluid system, and the cost differential can increase as much as 40% to 50%.
In addition, the cost of thermal fluid is another key consideration. Water bath heaters can have as much as 8 to 10 times more thermal fluid than a comparable thermal fluid system, resulting in hundreds of thousands of dollars of extra initial fluid costs. This fluid must also be maintained and replaced over time, further inflating the lifetime system cost.
The significant difference in fluid fill volume also means that the weight of the water bath heater is many times that of a comparable thermal fluid system. This affects foundation designs and can result in higher construction costs. Due to these factors, a hot oil heater can provide significantly lower operational costs compared to a water bath system.
Control & Turndown
The concept of a water bath heater is relatively simple — it functions as a large, liquid heat sink. The bath is maintained at a constant temperature and the process coil absorbs energy from the bath. However, this concept has several control and responsiveness limitations. For example, due to the large volume of fluid, changing the temperate of the bath liquid takes time.
The speed at which the temperature can rise is limited by the burner’s firing rate. When the burner is turned off, lowering the temperature is dependent on the process coil’s ability to remove temperature from the bath. In either situation, it can take anywhere from 30 minutes to several hours to substantially alter the bath temperature. For this reason, many water bath applications involve a process flow bypass valve to control process temperature while ensuring the bath temperature remains constant.
While this can be an effective control method, it is limited by the ability of the bypass valve. Since bypass valves don’t control well at the bottom end of their control range, if the process flow rate or temperature range varies by more than 10:1, this can pose a potential issue. In contrast to this type of system, a hot oil heater offers dynamic and responsive control. It features excellent turndown capability and quick response times. Since the volume of fluid in these systems is limited, system operating temperatures can be changed quickly. In addition, compared to water bath heaters, process turndown can be exponentially improved by implementing multiple heat exchangers parallel to one another.
Learn More About Thermal Fluid Heating Systems
Hot oil heating systems operate at higher efficiencies than water bath systems and can result in significant savings. Many applications that have traditionally been associated with water bath heaters can actually use a hot oil heater instead, with improved process control and turndown. If you’re considering purchasing a new thermal fluid hot oil heater, it can feel challenging to understand all of your equipment options.
At Sigma Thermal, we can help you learn everything you need to know about hot oil heating systems. Our team designs, engineers, and maintains process heating systems for many industries. We can help you obtain the innovative solutions you need at an affordable price. To get started, request a quote today or check out our eBook for more information.
Calculating your thermal oil heater’s efficiency may seem simple and straightforward, but in reality, simple calculations fail to account for all of the factors that play into the heater’s efficiency. This may cause you to overestimate a thermal heater’s efficiency and force you to pay more than you bargained for over time.
To avoid this expensive mistake, make sure to educate yourself on the nuances of thermal efficiency before investing in a new oil heater. Understanding these complexities will allow you to make informed decisions regarding which efficiency level you should target.
Basic Operation of Thermal Oil Heaters
The main advantage of thermal fluid heating is that it provides both high temperature and low pressure, making it ideal for industrial process heating applications. To achieve this temperature-pressure balance, thermal fluid heaters go through the following steps:
- A direct-fired heater warms the thermal fluid, which is specifically designed to capture and retain heat.
- This heated thermal fluid circulates to each of the connected components in a closed loop, transferring its heat to any number of users.
- The fluid returns to the beginning of the loop for reheating, and the cycle repeats.
The chemical makeup of this fluid will vary depending on the brand and type of thermal oil heater. Water and steam are the most basic options since water has such a high heat capacity, but many modern oil heaters incorporate organic media into their circulation fluid.
Calculating Your Unique Efficiency
Many manufacturers provide an efficiency measure with their products, but these are often sweeping generalizations that may not be accurate in your specific facility. To find the most efficient option for your space, you must have an understanding of efficiency principles and how they work for your specific situation.
For energy systems like thermal oil heaters, efficiency is determined by the ratio of thermal output to energy input. Although this may sound simple, there are hundreds of elements that factor into how much effect you get out of the energy you put in. One aspect that manufacturers often neglect, for example, is the flue-gas stack temperature and how that may affect your heat loss. Heat loss from chimneys is one of the greatest sources of inefficiency in thermal oil heating systems.
To account for this oft-neglected variable, we created a simple graph that shows the efficiency as a function of stack temperature—in other words, how efficiency varies as you raise or lower the temperature. Our calculations focus on the typical heater, which has 20% excess air and a 70° F (21.1° C) ambient temperature, and control for the other variables. If you know your stack temperature or can measure it directly, this graph is an extraordinary tool to help you see the effects of your flue-gas system on your heating efficiency.
“Is Your Thermal Oil Heater Truly Efficient?” eBook, by Sigma Thermal
Here at Sigma Thermal, we pride ourselves on developing and supplying unique process heating systems for a wide variety of industries. With an expert staff that has decades of experience, we are ready to provide an optimal solution to any and all of your heating problems.
For more information on the efficiency of your thermal oil heaters, check out our new eBook: “Is Your Thermal Oil Heater Truly Efficient?” Our latest eBook brings our expert knowledge directly to you. If you want to learn what goes into calculating efficiency and how to determine the efficiency of your equipment, this eBook is an excellent resource. Download your copy today!
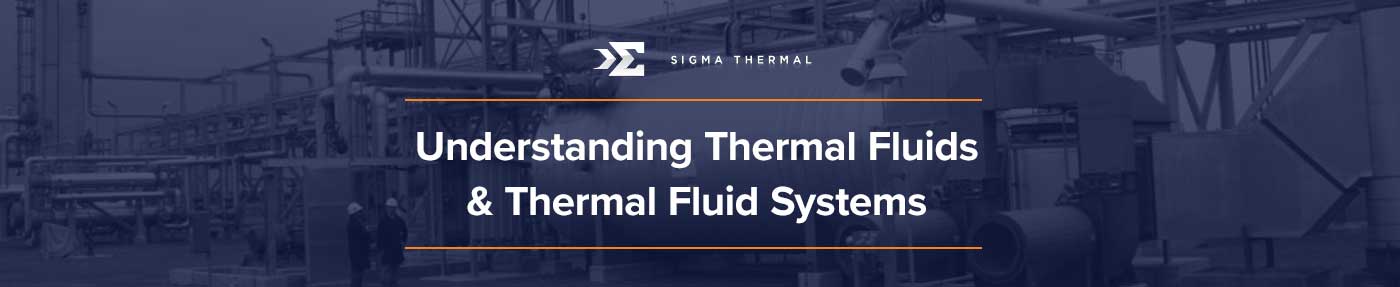
The demand for process heating and temperature control in the industry continues to increase as manufacturers and industrial facilities grow, expand, and seek to improve their existing operations. These process heating systems must perform consistently, safely, and with minimal downtime over time.
Industrial facilities that use plant-wide distributed process systems typically have one of two process systems: steam boilers or thermal fluid heating systems. Boilers were often the default choice in the past, but thermal fluid heating systems are a better solution for many applications, offering improved flexibility, control, and reliability.
Thermal Fluid Management
Thermal fluid heating systems operate in a closed-loop with the thermal fluid (also referred to as heat transfer fluid) in constant circulation. This continuous circulation at a constant supply temperature provides a heat source that users can access as needed. Users can be controlled individually, and thermal fluid temperature can be varied (user to user) through secondary control loops. In most systems, the thermal fluid or heat transfer fluid stays in a liquid state throughout the loop, although there are vapor phase fluids available for some niche applications that can benefit from latent heat over simple heat.
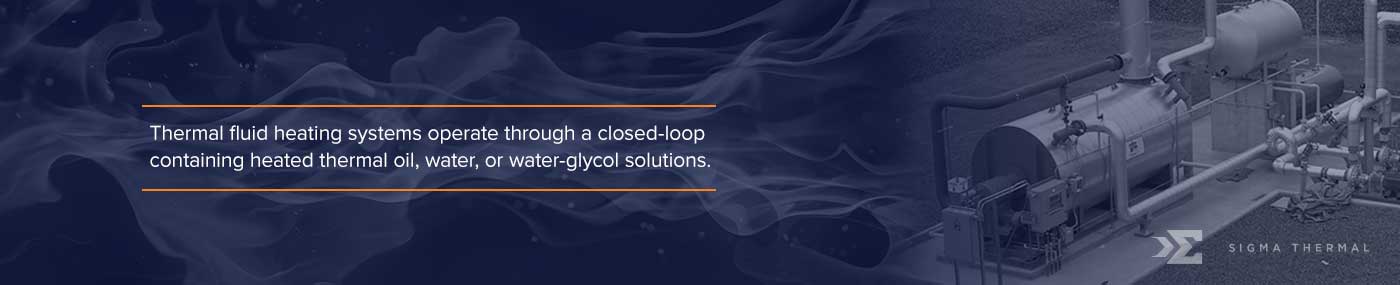
Types of Heat Transfer Fluids
Thermal oil, water, and water-glycol solutions are all commonly used in thermal fluid heating systems. All of these heat transfer fluids offer various advantages and disadvantages depending on the operating temperature and performance requirements of a system. It is important to understand what each fluid option is so a correct choice can be made for each application.
- Hot water and water-glycol. Water is the best possible heat transfer medium available when considering thermophysical properties, but it also comes with a number of drawbacks. Principally that it can be corrosive, contain contaminants, boils at 212ºF and freezes at 32ºF. Adding glycol in solution with water both increases the boiling point and decreases the freezing point, although that comes with some reduction in heat capacity.
- Thermal oil. Thermal oils tolerate higher temperatures than water-based formulas without boiling or unduly increasing system pressure. Natural oils can reach temperatures up to 600° F, while some synthetics allow oil-based systems to reach 800° F. These conditions allow oil-based heating systems to comply with ASME Section VIII, creating long-term savings since heat systems certified under ASME Section VIII don’t typically need a licensed boiler operator on site. Thermal oils are also typically non-corrosive and don’t need to be treated like water to prevent hard water deposits from forming in the system.
Advantages of Thermal Fluid Heating Systems
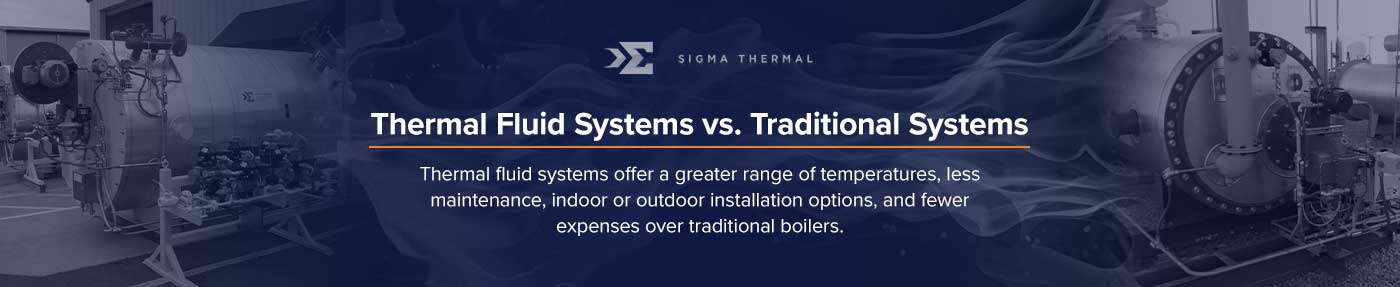
Thermal fluid heating, and thermal oil systems, in particular, have several advantages over their traditional boilers. These advantages include:
Achieving High Temperatures at Low Pressures
Thermal fluid systems offer a greater range of temperatures and a higher maximum temperature. These systems can reach temperatures of 0–750° F when using thermal oil, whereas steam-based systems only operate up to 350° F before operating pressures exceed 425 PSIG. Thermal fluid systems using water-glycol solutions can also reach 32–350° F at somewhat lower pressures than steam, which still offers significantly more flexibility than traditional systems.
While the temperature range is important, the low pressure is just as valuable. Most hot oils operating below 600° F don’t require any vapor pressure, and the maximum system pressure is only what is generated by the centrifugal circulation pumps. Even high-temperature synthetics operating as high as 750° F require less than 100 PSIG of vapor pressure. A steam system at 750° F would require over 3,200 PSIG of operating pressure.
Minimal Maintenance
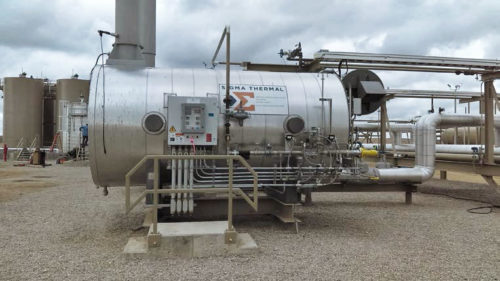
Aside from regular flashpoint tests, thermal fluid heating systems require relatively little maintenance.
The circuits are simple and the fluid doesn’t require frequent adjustments or additions provided it is cared for and tested periodically to identify any potential issues. Also, thermal fluid systems don’t need blowdown, re-tubing, steam trap maintenance, or water treatments like traditional boilers do.
No Attendant Needed
Due to the increased safety concerns regarding boilers near workers, more industrial, state, and local regulations require the presence of a stationary engineer in boiler rooms. Many plants across the country have to keep at least one employee with specialized training in the boiler room during active periods to monitor the boiler’s operation. This is most commonly required for fire-steamed boilers.
Facilities that use thermal fluid heaters and an unfired steam generator often don’t need a stationary attendant. This advantage depends on specific state and local requirements.
Outdoor Installation
Thermal fluid systems create indirect heating power, which means they can be installed in remote indoor locations or outdoors. Keeping the heater and primary system components away from other key production areas helps to improve overall plant safety.
Thermal fluid systems are easy to install outdoors, though there are additional installation considerations. Cold start provisions must be considered when sizing a circulation pump and motor. It may also be necessary to pour slabs, weatherproof outdoor piping and equipment, and more.
Utilize Central Plant Heating
Larger or multi-purpose facilities may have high-temperature processes in conjunction with open-loop steam injection requirements. Traditionally, these facilities would need a thermal fluid heater and a steam boiler. Today, however, these facilities can use heat exchangers and rely solely on the thermal fluid heating system instead.
Certain types of heat exchangers coupled with a readily available hot oil can produce near-instantaneous steam as thermal fluid flows into them. Operators may use this steam for sterilization, wash downs, and other processes. The advantages of a central plant heating system with a heat exchanger(s) include:
- Lower maintenance
- Fewer expenses (because there is no boiler)
- A heat system that achieves high temperatures at low-pressure levels
Types of Thermal Fluid Heaters
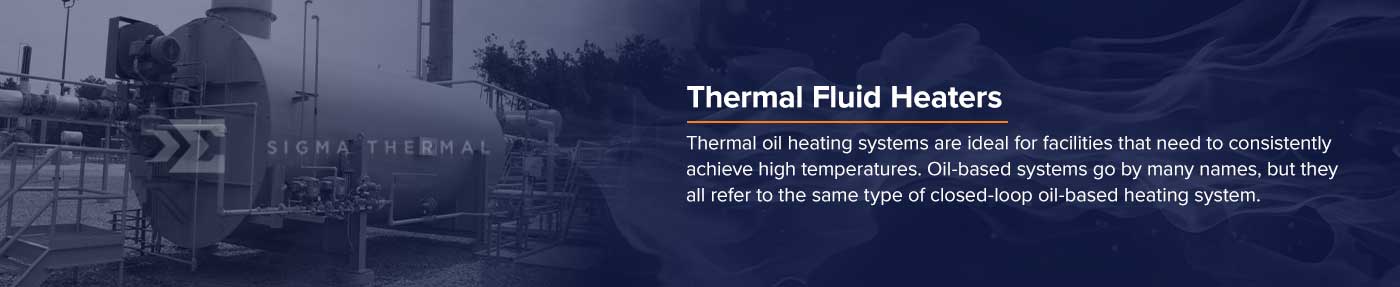
Thermal fluid heating systems are ideal for facilities that need to consistently achieve high temperatures. Oil-based systems go by many names, but they all refer to the same type of closed-loop oil-based heating system. Other common names include:
- Hot oil boiler
- Hot oil heater
- Hot oil system
- Thermal fluid heater
- Thermal fluid system
- Thermal oil boiler
- Thermal oil heater
- Thermal oil system
Of note, thermal oil-based systems are still often referred to colloquially as “boilers” even though they do not actually boil the process fluid. For closed-loop indirect heating systems with lower process temperature requirements, hot water and water-glycol mixtures are commonly used as heat transfer fluids.
Thermal Fluid Heater Options
At Sigma Thermal, our range of systems includes the following:
-
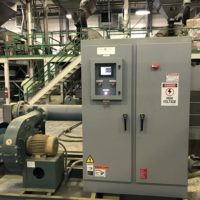
SHOTS Electric Heater

Thermal Fluid Heater
HC-1 Thermal Fluid Systems: These systems come in horizontal, vertical up-fired, and vertical down-fired options and the sizes range from 1–100 MM Btu/hr. Custom heater designs are available to meet specific project needs.
- HC-2 Thermal Fluid Systems: HC-2 systems are also available in horizontal, vertical up-fired, and vertical down-fired configurations. Sizes range from 1 – 100 MM Btu/hour and custom designs are available.
- SHOTS Electric Thermal Fluid System: Sigma Hot Oil Transfer Systems (SHOTS) use electrical power for circulation heaters and low-watt density immersion bundles. This creates heat without requiring fuel sources such as natural gas, fuel oil, or biomass fuel. These systems provide power in configurations from 30kW–800kW. Custom units can be constructed to provide increased power ranges from 800kW–4MW or even higher.
Biomass Fired Thermal Fluid Heaters: These heaters achieve the same high-temperature, low-pressure heat of our most popular thermal fluid systems. Facilities can use these systems alongside other biomass energy systems to meet green energy benchmarks. Sigma Thermal provides installation, training, and equipment servicing to support these systems and help our customers meet their sustainability goals.
Work with Sigma for Your Process Heating Needs
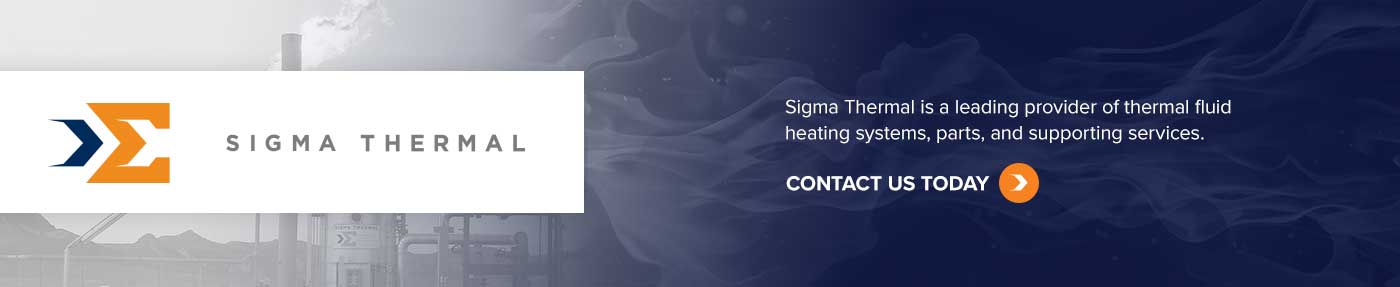
Sigma Thermal is a leading provider of thermal fluid heating systems, parts, and supporting services. We offer high-quality equipment that supports the energy, heating, and process needs of our customers in a broad spectrum of industries.
- Thermal fluid heating system installations
- Retrofit services
- Training
- Maintenance
- Part programs
Talk to our engineers and technicians today about your facility’s heating needs, including maintenance, parts, and full systems. Request a quote today to get your project started.
We are in the midst of a U.S. shale revolution: advancements in shale oil and gas extraction techniques have led to greater natural gas production levels and a renewed demand for natural gas in industrial and power applications. Because of the increased level of competition in the industry, process efficiency is paramount. Bringing natural gas to market cost effectively hinges on the optimal design and operation of the natural gas sweetening process.
Natural gas produced from reserves in almost never pure; rather, it contains acid gases such as carbon dioxide and hydrogen sulfide. One way to remove these impurities is amine gas treatment. An amine plant (also known as a sweetening plant) is used to remove the carbon dioxide and hydrogen sulfide from the gas solution so that pure natural gas can be efficiently transported to end users via pipeline.
Our latest white paper, Effective Heating Helps Amine Plants Purify Natural Gas, describes how to improve the natural gas purification process with effective heating. It also reviews the optimal conditions and system settings for controlling the amine regeneration temperature and optimizing the efficiency of the process.
The process works like this: the natural gas mixture and amine are combined in an absorber, where the carbon dioxide and hydrogen sulfide are removed. Pure natural gas exits from the top of the vessel and the amine is sent to a regeneration system (consisting of a still and a boiler) where it is filtered for reuse.
Usually, control and bypass valves are used to maintain a constant flow through the thermal fluid heater in the regeneration process. Moreover, the temperature of the system is typically controlled using overhead temperature measurements in the reboiler. There are a few problems with this standard procedure, which are described in detail in the eBook. If these problems are not addressed in the design of the control scheme, the process will not run optimally and the control systems could destabilize.
Using thermal oil as an indirect heat source can significantly increase the life of the amine solution and increase process efficiency. Typically, system operators manually set the flow of thermal oil through the reboiler. This is a convenient solution that prevents any need for frequent fine-tuning, but this conservative approach wastes energy. The eBook discusses the thermal fluid system specifications required to optimize the operation of amine plants.
Sigma Thermal has a long history of providing highly engineered process heating systems and fine-tuning services for existing systems. To learn more about Sigma Thermal’s expertise with amine reboilers, visit our website.
Download your free copy of the full eBook here or click on the button below.
Learn more about Thermal Fluid Heaters in Amine Plants
Retrofitting equipment can be a frustrating process if not planned and executed properly. Sigma Thermal has worked on a variety of retrofitting projects, including heater coil replacements, heater modifications, custom thermal system solutions and much more. To learn how Sigma Thermal can help you with your equipment, read on.
Case Study 1: Replacement and Repair of Thermal Fluid Heating System at a Biomass Mill
Specifics: J14090
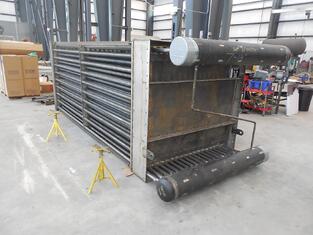
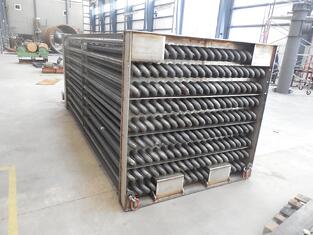
This project consisted of replacing 3 convection style tube bundles for a wood-fired thermal fluid system. Parts of the system were destroyed in a fire at a biomass mill.
Sigma Thermal has done a lot of work for this client before, so they had confidence we could deliver within the timeframe needed.
What We Did
Sigma Thermal engineered a temporary blind while still giving them access to the damaged equipment so it could be replaced. This allowed the customer to run half of their process and maintain
production with the other half of their system.
Case Study 2: Replacement of Two Natural Draft Burners
Specifics: J14099
This project consisted of replacing 2 natural draft burners with 2 forced draft burners, along with all the required supporting parts required to make the change. Once the project was installed, the service group went on site to fine tune the new burners. This change greatly reduced the start-up time for the heaters – as the purge time for a natural draft burner is near 15 minutes – where the forced draft is closer to 2 minutes.
What We Did
Sigma Thermal made required modifications to the heater lid, fuel train, electrical system, and controls, all of which were included in this project.
Learn More about Sigma Retrofits
Fire safety is an ever-present concern for operators of thermal oil heating systems. To understand the scope of the problem, let’s review the salient facts.
First and foremost, this is a relatively rare and well-understood threat to users of thermal oil heating systems. Plant owners and operators have been dealing with fire prevention issues for the better part of a century, according to an article in Chemical Processing magazine. So there are a lot of best practices in place to address this specific risk within the industry.
To discuss the parameters of fire safety in this context, experts rely on three measurements that describe fire phenomena: flash point, fire point, and autoignition temperature. Flash point is the temperature at which vapor from a fluid will temporarily burst into flame (or flash) when exposed to an ignition source. It’s measured by two tests approved by the American Society for Testing and Materials: ASTM D92 and D93. Fire point is the temperature at which such a temporary flame continues to burn the available fuel source. Fire point is typically 40-100°F above the flash point. Both flash point and fire point depend on the presence of an ignition source, such as a spark. Autoignition temperature marks the point at which no ignition source is necessary (as described by ASTM E659-78).
While the physical parameters described are important in understanding the fire risk of thermal fluids, they are actually more helpful to scientists in a laboratory than to plant managers and engineers in an actual chemical processing operation. According to the Chemical Processing article, “Relatively few fires have originated in thermal fluid systems.” Rather, the culprit in most cases is not the overheated thermal fluid but the equipment and systems conveying it. Specifically, blame can commonly be placed on poor choice of insulation materials, loss of flow, cracked heater tubes, or uncontained leakage.
What practical advice is there for such hazards? The complete answer is detailed in the article above, and in well-known industry installation guidelines such as FM 7-99, but here are a few highlights:
- Follow an industry accepted and widely used guideline, such as FM 7-99, to guide system design and installation decisions.
- Most good hot oil system manufacturers and hot oil fluid suppliers have published guidelines for installation and design that should be consulted as well.
- “The most effective precaution against insulation fires is the identification of all potential leak points and the specification of high-temperature closed-cell insulation or no insulation at these points.” Open cell insulation, such as fiberglass, will wick oil away from leak points and can potentially saturate hundreds of feet before a problem is seen.
- “To avoid incidents resulting from loss of flow, low-flow shutdown should be included in the burner safety interlock. . . ..”
- Use a low level alarm in your expansion vessel to notify an operator and shut down the system in the event that oil level in the system is falling below normal levels.
- Centralize major equipment and install containment berms in those areas to contain spills and isolate possibly incident locations when possible
- “To prevent excessive thermal cycling of the heater tube bundle, oversized heaters should be derated by the manufacturer.”
- “To prevent leaks, plants should: Allow expansion joints and flexible hoses to move along their axes, never sideways. Maintain lubrication systems for rotary unions and supply these systems with the correct lubricating oils. Install valves with their stems sideways so any leaks run down the stem and away from the piping.”
For more information on fire prevention practices for thermal fluid heating systems, contact one of our knowledgeable representatives or Application Engineers. We’ll be happy to answer your questions.
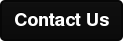